
Author Archives: allen

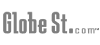
$30M-Plus Auction Yard Fueling More CRE Plans
September 4, 2008
$30M-Plus Auction Yard Fueling More CRE Plans
By Connie Gore
HUTCHINS, TX-With the final details now ironed out, the Allen Group Tuesday will break ground on its first build-to-suit in the 6,000-acre Dallas Logistics Hub in the southern sector. The milestone deal with Adesa Inc. for a 200,000-sf auto auction complex is opening “This is a very unique use. It doesn’t interact or feed off the intermodal facility or the rail lines. It’s a destination for car dealers,” says Daniel J. McAuliffe, president of Allen Development Texas LLC, “and it creates a tremendous need for hotels in the area.” Likewise, Adesa’s 175-acre tract at 3501 Lancaster-Hutchins Rd., secured by a 20-year lease with options, is expected to be a catalyst for brandnew retail and restaurant development in the corridor.
The San Diego-based Allen Group has peppered Dallas Logistics Hub’s master plan with eight hotels at two entrances to its land. McAuliffe tells GlobeSt.com that the hope is at least one hotel will be under construction at the eastern end when Adesa’s complex comes on line in July 2009 and $8 million of road and utility line infrastructure is finished.
We’re trying to identify what levels of service we want to have and the flags we want to have,” McAuliffe says. “There is a lot of interest from the hoteliers, but nobody has stepped up at this point.” The door is open to sell a site, a build-to-suit or an Allen-owned hotel with a management company to run it for the kick-off play. Meanwhile, city leaders are in talks with retail developers for a number of prime sites, he says.
For now, the focus is getting a showcase auction yard up and running for Adesa, which plans to sell its 50-acre hub at 1224 Big Town Blvd. in Mesquite, roughly 13 miles north of its new location. The same team that negotiated the build-to-suit lease is marketing the Mesquite yard–Bob Hagewood, vice president with Dallas-based Stream Realty Partners LP and Bob Ikel, an independent broker for IC3 Real Estate Consultants, also in Dallas.
Adesa will double in size when it’s time to relocate to the new yard, which will have 2,500 feet of frontage along Lancaster-Hutchins Road. With an all-in development cost topping $30 million, the complex will consist of an 80,000-sf auction arena, 110,000-sf reconditioning center, 10,000 sf for a tech center and car wash and parking for 22,000 vehicles for inventory, customers and employees.
The Carmel, IN-based Adesa, an acronym for Auto Dealers Exchange Services of America, runs 120,000 vehicles per year on a 50-week schedule through its Dallas shop, which opened in 1996. Adesa’s portfolio has 62 locations in the US, Mexico and Canada, with all four major metros in Texas in the mix. “Texas is one of the largest markets in the country and Dallas is the largest market in Texas,” says Warren Byrd, executive vice president of corporate development. “We are committed to growing our business in the industry and Dallas is long overdue for an expansion.”
Adesa Dallas is a regional auction yard for a 500- mile radius, crossing over the borders of Oklahoma, Arkansas and New Mexico. Byrd says Adesa also is expanding its Kansas City, MO yard, a 150-acre corporate-owned location that will be completed in January. In Phoenix, a search is on for a new site.
Byrd says Adesa Dallas will be similar in design to its San Francisco facility, complete with photography and inspection capabilities for institutional consigners and dealers. Architura Corp. of Indianapolis designed the Adesa Dallas complex and Shiel Sexton Co., also from Indianapolis, is the general contractor.
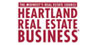
Kansas City Industrial Market
September 1, 2008
Kansas City Industrial Market
By Michael Block
Until recently, Kansas City has not been considered by big box industrial users as a regional distribution hub, in spite of it being home to four rail lines, having become the largest rail server in tonnage moved; three major interstates; the third largest trucking center in the nation; an international airport; and access to barge traffic on the Missouri River. Rail has a significant advantage in energy efficiency, capacity and cost effectiveness, and Kansas City is starting to see the big box users that for years were locating in other major metropolitan markets.
Story after story in the national press and trade magazines are now discussing Kansas City because the metro area now has approximately 2,000 appropriately zoned acres and four major industrial parks ready to hit the market in the next 6 to 24 months. With a population of more than 2 million and one of the faster growing metro areas in the Midwest, Kansas City is on the move. It has stable growth and approximately 255 million square feet of manufacturing, warehousing, distribution and flex industrial product, including its rather unique underground offerings. Currently, the industrial vacancy rate for the greater Kansas City market measures 7 percent.
The development community has been very conservative during the last few years and speculative development has occurred at a very measured pace. However, at mid-year, distribution centers that were targeting the Kansas City region included 19 large prospects, with six users seeking sites of more than 400,000 square feet and two whose space requirements exceed 1 million square feet.
Several new parks are coming online, with the first being the new Burlington Northern Santa Fe (BNSF) Intermodal Freight Hub in Gardner, Kansas. The Southwest Johnson County hub is to be located on 400 acres and accommodate 7 million square feet of warehouse space. In addition, The Allen Group will develop an additional 1,000 acres, which can accommodate between 8 million and 10 million square feet of distribution space. In addition, other related developments include the Sun Life Insurance Company, which with its fee developer, Kessinger/Hunter, is developing a new 600,000-squarefoot, state-of-the-art warehouse and distribution center in Olathe, Kansas, just 7 miles from the Gardner intermodal project. Scheduled for occu- pancy this month, it is the largest speculative building of its kind to be developed in Kansas. Also planned for development in Gardner is the Midwest Commerce Center, which LS Commercial Real Estate is developing in conjunction with USAA Real Estate. The industrial park’s first building, a 517,000-square-foot spec distribution center, is scheduled to break ground soon. When fully developed, Midwest Commerce Center will contain approximately 2.3 million square feet of bulk warehouse product.
The second major project is the Kansas City Southern (KCS) Intermodal Center, punctuated by KCS’s quest to develop a NAFTA-driven rail corridor from Kansas City to Mexico’s Pacific Coast. Being developed in conjunction with Chicago-based CenterPoint Properties, the rail-served intermodal facility will be situated on 340 acres, with 11,340 feet of rail track. In addition, CenterPoint, which acquired the former Richards Gebaur Air Force Base from the Kansas City Port Authority adjacent to KCS’s property, plans to build 5 million square feet of freight storage space on an additional 970 acres. The developer’s site is currently being upgraded and having infrastructure completed.
The third major project is the KCI Intermodal Business Centre, which is being developed by Trammell Crow Company on land owned by the Kansas City Aviation Department that is located adjacent to the Kansas City International Airport. In a related development, the SkyPort Business Park is underway near the Business Centre; its owners began grading 160 acres and have already sold 47 acres to Pure Fishing, which will construct a new 400,000-square-foot distribution center. With its prime location on airport property, including some parcels with on-ramp access, and Foreign Trade Zone status, the business center will appeal strongly to logistic users that may benefit from a close proximity to an international airport, as well as nearby Interstate 29.
In Riverside, Missouri, in the center of the metro area, Block & Company is developing the Horizons Business Park. Situated on 400 acres at Interstate 635 and Highway 9, the park will feature more than 5.3 million square feet of industrial space when complete. Unlike the other developments, it will be a mixed-use, master-planned business park community, offering an array of services. The park’s central location will help draw labor amid the area’s growing proliferation of industrial development. Some land will be available for sale; however, the majority will be for speculative development for lease.
Other active developments in the Kansas City metro area include the city of Olathe joining forces with Kansas State University to catalyze the development of 92 acres at K-7 and College Boulevard. The project, recently named the Kansas Bioscience Park recently secured its first tenant; Fort Dodge has plans to build a 150,000-square-foot research and development facility within the park. This region is supported by some of the top animal health education programs in the nation, with a collection of universities in Missouri, Nebraska, Kansas and Iowa playing key roles and having some of the top animal health programs in the country. Growth in this industry will be another catalyst for future growth for the warehouse and flex market in the area.
OPUS Northwest, Watkins & Company and Prime Investments are all developing, or have recently completed, new buildings in the Kansas City market. Prime’s building at Interstate 70 and 7th Street in Kansas City, Kansas, has been leased by Line, a supplier to the nearby and highly successful GM Fairfax plant, where the Chevy Malibu is built.
Block & Company is also active at the College Crossing Business Park, where it just completed the development of four buildings, totaling 160,000 square feet. In addition, three more buildings will break ground in the near future and offer an additional 280,000 square feet of distribution space.
During the next several years, analysts expect that the rail line traffic will continue climbing, with the increase in offshore manufacturing and rails efficiency edge over trucking, along with the public frustration toward highway congestion. Industrial developers will select locations close to intermodal hubs to take advantage of the cost of transporting goods. With these factors in place, it appears that trends to larger, centralized warehousing and distribution centers will continue for the foreseeable future and Kansas City is well positioned to capitalize on these trends.
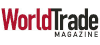
Will the Oil Crisis Fuel Near-Sourcing?
September 1, 2008
Will the Oil Crisis Fuel Near-Sourcing?
By April Terreri
As the escalating oil crisis unfolds, companies with long, complex global supply chains are reevaluating whether their Asia-based networks still make economic sense.
Pete Sinisgalli, president and CEO of Atlanta-based Manhattan Associates, reports that at a recent conference sponsored by AMR Research, supply chain leaders from around the country met to discuss key issues facing the industry. “The No. 1 topic was the increasing transportation costs, whereas in the past number of years the leading topic had been supplier performance.” High on the agenda of management decisions associated with transportation costs are the net value of extended global supply chains. This is prompting reevaluations whether near-sourcing offers a solution to ease the pain and an alternative location for U.S.-bound goods currently coming from China and the Pacific Rim. With about 65 percent of the country’s population residing in the east, near-sourcing from Mexico, Central and South America certainly offers an attractive advantage of not having to ship crosscountry from ports like Los Angeles or Long Beach.
As with any incipient change, some hesitate to conclude that near-sourcing is a long-term trend to reckon with. Denver-based ProLogis, for one, which pays close attention to customers’ changing supply chain needs, remains uncertain. “To date, we haven’t seen any of them make wholesale changes to the location of their facilities as a result of the run up in fuel costs,” notes Mike Peters, first vice president of global services.
Others like Greg Aimi have a different view. Nearsourcing is definitely an escalating and emerging trend, notes Aimi, director of supply chain research at Boston-based AMR Research. “I think it’s still in its infancy, but the cost of oil is causing it to be more acute.” Aimi adds that in the first six months of 2008, AMR Research saw a significant demand for network design studies, beyond what researchers were expecting. “People are concerned about risk mitigation strategies and continued congestion issues at the Port of Los Angeles. So people are very sensitive to the effects of the outsourcing model.”
‘Green’ also figures in the strategy. Companies can reduce their carbon footprint by choosing nearsourcing. “Everything associated with sustainability is very real,” continues Aimi. “We see many of our clients already asking us to include this as part of their planning and decision-making process.”
Regardless of whether this is a sea change or not, supply chain executives are taking a harder look at their manufacturing and transportation costs in an attempt to contain total landed costs. “With oil at $150 a barrel, you have to ask the question if it makes sense for you to manufacture locally in order to cut down that transportation piece,” suggests Neil Doyle, executive vice president of infrastructure and transportation development for Chicago-based CenterPoint Properties. The firm owns, acquires, and develops industrial real estate and related rail and port infrastructures, owning 45 million square feet of distribution space on 8,000 acres in the Chicago market. “You need to determine if this new model overrides the cheaper overseas labor manufacturing coupled with the longer transportation run.”
Near-sourcing reduces some uncertainties and security concerns related to overseas manufacturing and transportation, continues Doyle, pointing to Wal-Mart’s surge of near-sourcing in NAFTA countries. “With fuel costs up, the old model of entering an LA port and then getting products where they need to go is being replaced by entering at the port closest to your consumption base. This means the Southeast ports since the majority of the population is east of the Mississippi.”
CenterPoint developed a number of on-tarmac airfreight facilities, including several at Chicago’s O’Hare Airport. “We rolled that concept into developing intermodal centers across the country with the theory being to locate your DC next to the rail terminal via the inland port model, which is no different from locating your DC next to a maritime port,” says Doyle. “You get more certainty and substantially reduced cost in your supply chain because you eliminate the dray movement from the port to your warehouse.”
Doyle notes DC locations are shifting closer to populated centers than was true in previous years. “The day of the DC located in less-populated areas with cheap or free land is being replaced by the population-center model. What is also coming into play now and revising the supply chain as we know it is the cheap U.S. dollar, which means it might make sense to manufacture goods in the U.S. now more than anytime in the past ten years.”
Manhattan Associates reports seeing more companies reevaluating where they source product. “Manufacturing U.S.-consumed products in China added time and transportation expenses, but saved on factory labor,” says Sinisgalli. “Now that transportation costs are escalating, companies are reexamining questions such as, ‘Do I manufacture jeans in China or am I better off manufacturing them in northern Mexico to reduce my transportation costs?'”
While some companies are still evaluating the changing supply chain landscape, others are beginning to make moves to near-source. But no one can change their supply chain models overnight and it will take some companies time to work through the process. “Most thought-leading companies continuously examine their supply networks to refine where they would like to be in two or three years so that as they make changes today, they are in line with their desired future end-state,” says Sinisgalli.
Economics of proximity
Certain product groups make economic sense to produce in or near the consumption-market country, notes AMR’s Aimi. “Products with a volatile demand that is difficult to predict, such as apparel and consumer electronics, are the ones that should be looked at for near-shoring first.”
For example, a computer company might make components in bulk and ship them to a fulfillment center close to markets, where each computer is configured according to unique customer requests. “A retailer like Best Buy might have 10 different choices of a product on their shelves,” explains Aimi. “They can monitor to see which ones are selling so they can issue a slowdown or speed-up to the manufacturer, based on demand.”
Chainalytics reports it is noticing another pattern among clients. “It is a strategy called postponement – or delaying for as long as possible the forward deployment of products to as close to customers as possible, holding product back further down-stream in the distribution network,” explains Jeff Metersky, vice president of supply chain strategy practice for the Atlanta-based firm. “Since they don’t know for certain what customer demand will be, they will hold back until they receive the final demand signal that allows them to move products to customers.”
Companies are also containing costs by increasing inventory–depending on the nature of the products, reports Metersky. Remember when holding inventory was a bad thing? That strategy is changing to accommodate rising fuel costs. By pushing more inventory into the network, companies can reduce transportation spend by shipping larger shipments or by shipping via more fuel-efficient and costeffective modes.
One of the trade offs companies have wrestled with over the years has been the balance between transportation costs and inventory costs. “JIT inventory management was a beautiful thing when oil was cheap,” explains Sinisgalli at Manhattan Associates. “In some cases, holding larger inventories but making fewer deliveries will be the future strategy.”
Backhauling will be a top priority to avoid running empty miles. Sinisgalli points to industry studies that conclude that over 10 percent of the 150 billion miles U.S. truckers drive annually are driven empty. “So you can look at this from an environmental perspective as well as from a cost perspective for motivation to develop opportunities to do things more efficiently.”
As this trend evolves, companies are thinking about changing their network configuration to include more and smaller warehouses close to drop-off points in an attempt to maintain service levels while reducing transportation costs, adds Sinisgalli. “You will still have the large warehouses around the ports of entry, which will remain the most efficient places to handle goods.”
Metersky at Chainalytics adds that what changes the distribution network is the amount of inventory flowing from ‘the make’ to ‘the buy.’ “The demandpull signals first indicate what is selling where and then they determine where the DC should be located. As sourcing patterns change, so will the driver as to where those DCs are located.”
So where does one begin in changing already established networks? Companies need to conduct a network optimization assessment to simulate demand when to consider moving to a near-sourcing model. The manufacturing location should be close to rail and intermodal access. State taxes, labor costs, and real estate costs should be factored into the assessment. “Companies should understand what their inventory holding costs and transportation costs will be with respect to satisfying customer demand,” notes AMR’s Aimi. “Don’t forget to add in the realities of state and local taxes. Know the labor market and the cost of that labor, as well as real estate costs. These are additional factors you must represent when you model because if you leave them out of the modeling process, they could foil your entire plan.”
Drayage costs are key for deciding where a DC should be located, yet they are often overlooked, notes Bob Liss, vice president of supply chain for The Allen Group in Dallas. For instance, a company with a DC located in a logistics park adjacent to a rail terminal that is importing over 100 containers per week can save millions of dollars a year on inthe- gate shuttle costs–versus over-the-road drayage costs to points outside the logistics park.
Liss adds that drayage costs will only get worse. He reports rising gas prices caused 1,000 truckers to go out of business during the first quarter of the year, with another 2,000 expected to do the same by the end of the second quarter of this year. “With this capacity taken out of the market, trucking rates for drayage are expected to rise between 8 percent to 10 percent by the fourth quarter.”
Another strategy helping companies contain total landed costs is deconsolidation, notes Dave Ganor, vice president of Business Development for Contract Logistics at Pittsburgh-based GENCO Supply Chain Solutions. “We are seeing more requests for deconsolidation centers, not only at the major ports of entry, but at secondary ports as well in the nearsourcing strategy.”
Although Ganor reports GENCO has noticed some near-sourcing movement, he says deconsolidation strategies continue to drive the networks of larger global customers. Goods are received at a transload center where they are reconsolidated into full trailer loads in response to updated demand. “They are shipped via truckload or intermodal, depending on which mode is more cost effective. Deconsolidation strategies are popular because shipping containers inland is an expensive proposition. Then you have to worry about repositioning those empty containers.”
Inland ports
Rail-based freight drove the development of inland ports from about 1995 through 2005, explains Robert Harrison, economist and research scientist at the Center for Transportation Research at the University of Texas at Austin. Rail double-stack transcontinental services, particularly serving West Coast ports, soon carried large volumes of containers destined not just for northeastern markets, but to terminals serving cities like Dallas, Kansas City,
Memphis, and Chicago.
“So the notion was to take commodities to one centralized metropolitan site and deliver product to DCs close to these new terminals,” Harrison explains. “They are multi-modal, value-added centers that come in all shapes and sizes, and are really streamlining the importation process for containerized products originating from primarily Asia.”
Inland ports do more than just duplicate port or gateway functions at inland locations. They concentrate transportation and logistics services, helping transportation planners to promote economic development through logistics integration. Some value-added services include light manufacturing, as in the case of Hillwood’s Alliance Texas in Fort Worth.
“This was one of the early successful and fastgrowing centers with a large BNSF terminal, airport, and interstate access that attracted a variety of DCs and logistics services,” Harrison reports. “They now provide a whole range of services to support DC operations and the efficient movement of goods. When DC efficiency was impacted by labor turnover due to the long commute from Dallas, Hillwood constructed a housing subdivision, together with associated services. It is a planned community rather than a terminal in the traditional sense.” The development now includes high-end homes, an air cargo facility, medical facilities, and shops.
Nokia’s near-souring arrangement at Alliance is a good example of how inland ports can expedite product manufacture. A few years ago, the company had a two-prong approach, with components coming in from both Singapore and Mexico. “They had regular service from Singapore on Lufthansa into Dallas-Fort Worth and they would near-source everything else based on their daily order requirements,” Harrison says. Black & Decker has a similar arrangement, utilizing the border maquiladoras along the U.S.-Mexico border. Imports from Mexico still tend to be trucked, although the Mexican rail system is being strengthened. Kansas City handles both Asian and NAFTA commodities and is a major proponent of the inland port concept to the point where they are negotiating to have a Mexican customs facility to handle inbound NAFTA commodities, reports Harrison.
Whether products are coming from Mexico, Central America, or China, they must move efficiently from the border into the heartland. “The price of fuel is driving the long hauls away from truckers to stacktrains, which will terminate at a few inland intermodal terminals,” explains Liss at The Allen Group. Companies with DCs at logistics parks adjacent to intermodal terminals in key distribution cities like Chicago, Dallas, and Kansas City can save on the cost of moving containers.
The Dallas Logistics Hub, developed by The Allen Group, is preparing for opportunities existing in that market. Its location, on 6,000 acres, will benefit from the proximity of two Class 1 railroads, four major interstates, and Lancaster Airport, which will become an air-cargo facility. Its plans include mixed-use development and will have 60 million square feet of distribution, manufacturing, office, and retail space.
“When the Panama Canal is widened, the Port of Houston traffic can truck right up to Dallas,” says Liss. “And three miles west of the hub’s western boundary is I-35, which is the NAFTA corridor going down to Laredo. So it is ideally located for Mexican imports.”
Bringing international containers to Dallas where they can transload into domestic containers will help balance the network while achieving better total landed costs, explains Liss. “You are closer to the eastern markets and you have carriers looking for backhauls, so the economics are there. You have to be loading in both directions, so you can create domestic capacity with import loads and then turn the boxes around with export cargo.” He notes that the cotton industry is one major segment looking for export boxes. Anticipating increased export volumes, Liss recently met with container leasing companies to negotiate a supply of guaranteed containers into Dallas.
The railroads are investing in updated infrastructure to handle increasing volumes in their high-density lanes. “Railroads are improving their tracks to be service-competitive with trucks,” says Liss. “BNSF and UP are double-mainlining high-density intermodal corridors. This will increase their capacity and improve service.” He adds that Norfolk Southern is investing millions into the Meridian Speedway to connect into Dallas from Meridian, Mississippi and KCS has invested over a billion dollars in its rail lines in the U.S. and Mexico.
Down the road
An area to watch, notes Harrison, is the rise in U.S. exports. “We will begin to think about inland ports as part of the supply chain that works in both directions. With the falling dollar and the growth of exports requiring containerized boxes, there will have to be a bit of fine-tuning of the supply chain.”
In conclusion, it is accurate to say that the global supply chain is flexing at the moment, although slowly. “The cost of fuel is definitely affecting the supply chain,” says AMR’s Aimi. “We now have to contend with higher fuel costs after the overzealous approach to moving to China. This is causing volatility in the network so we have to reassess our move to China.”
Europeans have faced high fuel prices for years and have continually adapted their supply chain networks, inventory levels, and transportation functions to improve operating performance, reminds Sinisgalli at Manhattan Associates. “So there are parallels between what Europeans have already adopted and what the U.S. will likely evolve to. As the microeconomic landscape shifts rather radically, we will see companies that adapt to rising fuel prices with better-optimized supply networks achieve a competitive advantage
The Allen Group Hosts Official Groundbreaking Ceremony for ADESA
The Allen Group Hosts Official Groundbreaking
Ceremony for ADESA
The First Build-to-Suit Tenant at the Dallas Logistics Hub
DALLAS, TX. (August 27, 2008) — The Allen Group, developer of the Dallas Logistics Hub, will hold a groundbreaking ceremony for ADESA’s new state-of-the-art auto auction facility on Tuesday, September 9, 2008 at 2:00 p.m. The build-to-suit facility will be located on 175 acres within the City of Hutchins. The property will house three buildings totaling approximately 196,000 square feet of space for an auction arena, administrative and financial offices and reconditioning facilities. Below is further information about the event:
WHAT: Groundbreaking Ceremony
WHO: Artis Johnson, Mayor, City of Hutchins
Richard S. Allen, Chief Executive Officer, The Allen Group
Daniel J. McAuliffe, President, Allen Development of Texas
Tom Caruso, Chief Operating Officer, ADESA
Warren Byrd, Executive Vice President of Corporate Development,
ADESA Pat Stevens, Regional Vice President, Western Region,
ADESA
WHEN: Tuesday, September 9, 2008
2:00 p.m. – 3:00 p.m. (Program)
WHERE: ADESA Construction Site
3501 Lancaster-Hutchins Road
Hutchins, Texas 75141
(Directions: See Attached Map)
VISUALS: State & Local Elected Officials
Ceremonial Shovel Dig
Construction Site
Construction Equipment & Trucks
ADESA offers a full range of auction, reconditioning, logistical and other vehicle-related services to meet the remarketing needs of both its institutional and dealer customers. With 62 auction locations in the United States, Canada and Mexico, strategically located near metropolitan areas with a large concentration of used vehicle dealers, the company is well positioned to host both physical and Internet auctions. Through its related subsidiaries of AutoVIN® and PAR North America, it is also able to provide additional services including inspections, inventory audits and remarketing outsourcing solutions including a network of repossession agents, titling and auction sale representation.
The Dallas Logistics Hub is the largest new logistics park in North America with 6,000 acres master-planned for up to 60 million square feet of vertical space for distribution, manufacturing, office and retail uses. This premiere logistics facility is adjacent to Union Pacific’s Southern Dallas Intermodal Terminal, a potential BNSF intermodal facility, four major highway connectors (I-20, I-45, I-35, Loop 9) and the Lancaster Airport, which is in the master-planning stages to facilitate air-cargo distribution.
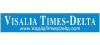
Many companies still using trucks
August 23, 2008
Many companies still using trucks
By VALERIE GIBBONS
Developer Richard Allen went to great lengths to build two San Joaquin Valley industrial parks next to railway lines, just in case a company wanted to use the line for its distribution.
In 15 years he hasn’t had any takers. It’s not that the Allen Group’s West Visalia and Shafter parks aren’t thriving — they are — it’s that the Central Valley’s 300 mile-long span between the major urban centers of San Francisco, Sacramento and Los Angeles is too short to be an efficient use for rail.
“Using rail to go 200 miles is like using a semi-truck to go 100 feet; it’s just not competitive,” Allen said. The Allen Group’s MidState 99 Distribution Center in west Visalia has 2 million square feet of space, all occupied. Current tenants include VF Corporation, International Paper Company, JoAnn Stores, Coast Distribution Systems, Workflow One, Worms Way, Bound Tree Medical, ORS NASCO and DATS Trucking.
All of the companies use trucks to ship their goods. The scene is much different at the Allen Group’s other parks in Dallas and Kansas. There, major retailers are building towering warehouses and distribution hubs stretching millions of square feet simply because of the rail lines. “They have to be there,” he said. “Because if their center is 30 miles from the railway, they need to load it onto a truck and ship it in — and that’s inefficient.”
But with the rise in fuel prices that business model may be changing —at least for bulk items such as lumber, steel, coal, sand and agricultural products. Zoe Richmond, a spokeswoman for Union Pacific Railroad — which runs trains along the east side of Highway 99 — says traffic has been up nationally this year.
“Our commodity shipments have been up,” she said. “But our other traditional customers who ship containers or cars have been down.” Union Pacific saw its profits rise 18 percent this year. Burlington Northern Santa Fe’s profits from freight were up 16 percent.
It’s a mixed blessing for Tulare County. While more companies are moving to rail to ship their goods through the Valley, the trains don’t stop in Visalia. That leaves the vast majority of the area’s imports and exports moving by truck.
Truck emissions
Officials with the San Joaquin Valley Unified Air Pollution Control District said emissions from heavy- and medium-duty trucks account for 17 percent of the Valley’s air pollution. By 2020, daily truck traffic will grow from today’s average of 18,760 trucks a day to 37,500 trucks a day, the air district said.
That pattern won’t change any time soon for some east county businesses. Reliability and accountability issues have left many orange growers shipping their product by refrigerated truck.
“It’s a perishable commodity and it’s imperative that it get there quickly,” said Bob Blakely, the director of grower services for California Citrus Mutual. Although oranges have a longer shelf life than a tomato or a peach, local orange growers switched from using rail to trucks once the modern highway system came of age. Today, growers can truck their products to anywhere within the country in a matter of days.
“It can make it there within the same time period by train but you never know when it’s going to be parked on [a side track] somewhere for a week,” he said. “The more time it spends in shipping, the higher the rate of decay. If railroads were more reliable that would be a be big hurdle. Rail would be a lot more attractive.”
One New York-based rail company is hoping to bridge that gap. This June Railex, LLC, began building a 200,000-square-foot cold storage facility just off of Highway 99 in Delano. The company plans to ship agricultural commodities east on its own 55-car train to the company’s warehouse in Rotterdam, N.Y. Railex plans to hire 300 people.
The company’s literature says it will guarantee shipments to New York within five days.
Officials with Railex did return calls for comment bypress time.
But it may take more than a one company’s efforts to make rail a priority for local growers.
The problem: Blakely said even though many growers ship overseas to Asian markets, they still use trucks to get the oranges to the ports.
“The oranges can be in-route for up to 14 days but then again they have a higher tolerance for what’s allowable in their products.”
But even if more of those goods were to be shipped to California’s ports by train, Allen said right now the railroads don’t have the capacity to accommodate a whole new class of freight.
“The railroads are making money for the first time in 30 years,” Allen said. “They’re moving a lot more non-containerized goods.
“The problem is that it’s not happening to and from Visalia.”
Rail cars, left, await being coupled by an engine, right, on the San Joaquin Valley Railroad lines Thursday along Goshen Avenue on the west side of Visalia.
Truck traffic in the San Joaquin Valley accounts for:
-
87 percent of the goods shipped out of the Valley
-
81 percent of the goods shipped into the Valley
-
50 percent of all commodities shipments
-
24 percent of all of the traffic on Highway 99
-
30 percent of all of the traffic on Interstate 5
Source: San Joaquin Valley Unified Air Pollution Control District
-
U.S. railroads originated 1,606,877 carloads of freight in July 2008, up 16,825 carloads (1.1%) from July 2007.
-
Number of railroads: 24
-
Shipped 7.5 million carloads of freight
-
Food products: 9 percent
-
Primary metal products: 5 percent
-
Glass/stone: 5 percent
-
Chemicals: 5 percent
-
Mixed freight: 54 percent
-
Other: 21 percent
Source: The Association of American Railroads
Truck traffic in the San Joaquin Valley accounts for:
-
87 percent of the goods shipped out of the Valley
-
81 percent of the goods shipped into the Valley
-
50 percent of all commodities shipments
-
24 percent of all of the traffic on Highway 99
-
30 percent of all of the traffic on Interstate 5
Source: San Joaquin Valley Unified Air Pollution Control District
-
U.S. railroads originated 1,606,877 carloads of freight in July 2008, up 16,825 carloads (1.1%) from July 2007.
-
Number of railroads: 24
-
Shipped 7.5 million carloads of freight
-
Food products: 9 percent
-
Primary metal products: 5 percent
-
Glass/stone: 5 percent
-
Chemicals: 5 percent
-
Mixed freight: 54 percent
-
Other: 21 percent
Source: The Association of American Railroads
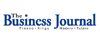
Tular County Growth Hitting the Target
August 8, 2008
Tular County Growth Hitting the Target
By BoNhia Lee
The efforts of Tulare County cities to bring in more jobs and increase shopping opportunities are starting to bear fruit Tulare County is known for its annual three-day World Ag Expo, which attracts agricultural enthusiasts and businesses from all over the world.
Last year’s expo attracted more than 1,600 exhibitors and 100,000 visitors, including 1,500 people from 74 different countries. The event generates an annual economic impact of $1.2 billion.
But what happens in Tulare County the other 362 days of the year when eyes are not focused on the world’s largest agricultural event?
That’s when Tulare County cities work on expanding their communities and providing more jobs as well as increased entertainment and shopping choices for their, residents.
That work is paying dividends. The county’s industrial sector has flourished, and retail businesses are filling new shopping center developments. Tulare County roadways are also finally getting a long-awaited facelift.
Location, location, location
Tulare County’s prime location near a main railway corridor and Highway 99 makes it an excellent place for large distribution centers to locate and do business.
Despite the challenging economy, the industrial market remains solid in Tulare County, according to a recent report released by Grubb & Ellis.
In May, The Allen Group, a commercial, office and retail developer, completed two 140,000-square-feet buildings for lease and a 252,000-square-foot distribution facility for International Paper Company at its Midstate 99 Distribution Center in Visalia.
Another 157 acres at Plaza Drive and Riggin Avenue in Visalia is in the process of being annexed to the City of Visalia for industrial development. The City of Tulare is also moving forward with annexation of 280 acres for a business park, according to the report.
“The Central Valley is really becoming an emerging location for distribution for the West Coast,” said Jon Cross, director of marketing for The Allen Group.
Cross said large companies are shifting their focus away from doing business in congested places like Los Angeles, where the cost of leasing space is $io-$i5 per square foot compared to $3-$4 per square foot in the Central Valley.
Companies are starting to realize the biggest benefit in Visalia, especially at the Midstate 99 logistics park, is the location. Cross said. The facility is in a UPS regional hub, allowing companies to distribute goods overnight to 98 percent of California at UPS’ ground rate.
The MidState center has 11 buildings totaling more than 3 million square feet. Current tenants include VF Corp., International Paper Company, Jo-Ann Stores, Coast Distribution Systems, Workflow One, Worms Way, Bound Tree Medical, ORS Nasco and DATS Trucking.
There are still 200 acres of land remaining in the park for future building opportunities, which would allow for additional buildings up to a million square feet.
“One of the unique things about the Central Valley, especially the Visalia; and Tulare County area, is the fact it is benefiting from not being overdeveloped,” Cross said. “There is strong labor, low real estate costs and a great infrastructure system.”
The growth of the industrial sector helps to create jobs in the county, said Jim Claybaugh, executive director of the Visalia Economic Development Corp. More than 5,000 people are employed by different industrial park firms in the area, he said.
Most of the jobs are entry-level positions, so companies can hire people with fewer job skills, then give them training and an opportunity for more upward mobility, Claybaugh said.
Shoppers get more choices
Tulare county residents no longer have to travel to Fresno or other bigger cities to do their shopping. Big-name retailers are setting up shop in town. The southern section of the City of Visalia along Mooney Boulevard has seen a lot of commercial development in the last few years, Claybough said.
The Packwood Regional Shopping Center spans 35 acres along both sides of the street. It’s anchored on one side by Lowe’s Focus I 9 and Best Buy and on the other side by Target.
Retail development has also spread to the city’s poorer north side, where a Lowe’s store anchors a shopping center at Demaree and Riggin avenues. Meanwhile, a new Target store is expected to open this fall at the Orchard Walk East shopping center at Dinuba and Riggin avenues. Sportsman’s Warehouse, a fishing and hunting retailer, is also scheduled to open a store there.
The City of Dinuba has worked on positioning itself as a regional retail center for the last five years. City leaders want to provide residents with 75-80 percent of their retail and entertainment needs within a 10- minute driving radius.
“We’ve put a lot of effort and energy into building our retail center and providing diversity in the kinds of retail options that are here for people, so they don’t have to make that longer drive to Visalia or Fresno,” said Dinuba City Manager Ed Todd.
Right now, Dinuba officials estimate residents are able to carry on about 65 percent of their shopping and entertainment activities within the city.
In 2006, the town’s Wal-Mart at El Monte Way was expanded into a Super Wal-Mart. The store added 60,000 square feet of pace to sell grocery items. The expansion also created 100 new jobs.
Entertainment is also available closer to home with the recent opening of the 18-hole Ridge Creek Dinuba Golf Club. “I think we’re having quite a lot of success in achieving that goal,” Todd said, “and we’re going to continue building on it.”
Measure R funds kick in
Road improvements, using Measure R funds are scheduled to begin this month to help alleviate traffic congestion along several roadways in Tulare County.
Measure R is a one-half cent sales tax passed in 2006 that will generate more than $652 million to ad- dress the county’s major transportation needs in the next 30 years.
Fifty percent of the funds will go to improve freeway interchanges, add lanes and increase safety. Another 35 percent will be spent on improving each city and the county’s transportation system, which includes pothole repair, repaving streets, bridge repair, traffic signals and sidewalk improvement.
About 14 percent will be spent to improve public transit programs such as the addition of bike lanes and air quality improvements. The last one percent goes to the Tulare County of Association of Governments to administer Measure R.
“It’s a really exciting time, because we’re getting that first glimpse of what we can do with Measure R regionally,” said Ted Smalley, executive director of the Tulare County Association of Governments, in the organization’s newsletter.
The first regional project to be funded by Measure R begins this month with a signal installation west of Dinuba at Avenue 416 and Road 56.
Later this month, two other regional projects will begin. One is the construction of the Santa Fe overpass in Visalia. The $i2.6-million project will open a major north and south corridor.
A second project is the widening of Road 80 to alleviate traffic between Dinuba and Visalia. According to traffic counts, about 6,000 vehicles use the road daily. The project will widen the road to four lanes from Avenue 304, also known as Goshen Avenue, to Avenue 328.
Other road projects coming up within the next year include: The widening of Scranton Avenue and Indiana Street in Porterville, improving the Ben Maddox overpass in Visalia, installing traffic signals west of Farmersville at the corner of Avenue 280 and Road 156 and conducting a study of the Avenue 416 bridge in Dinuba.
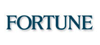
North Texas
uly 21, 2008
North Texas
By Susan Caminiti
Three months ago, Dallas Mayor Tom Leppert led a delegation of city officials and local business leaders on a weeklong visit to China. The April trip had many highlights, most notably meetings with Chinese officials in Beijing, Tianjin, Qingdao, Shenzhen, and Hong Kong. At each stop the Mayor presented a detailed overview of his city’s attributes: everything from its central U.S. location, proximity to a world-class international airport, and good demographics to its favorable business climate and solid commercial and residential real estate markets.
The sales pitch worked: At the end of the visit, ZTE the giant telecom company based in Shenzhenannounced it would establish U.S. headquarters in Dallas, bringing with it nearly 100 new jobs to start and an initial $1 million to outfit its 21,000 square feet of new office space. With China now Dallas’s top trading partner, the hope, says Mayor Leppert, is that ZTE is just the first of many Chinese companies that will be calling “Big D” their U.S. home. “We can’t afford to think of business on just a national scale, or even limit our efforts to this hemisphere,” says the Mayor, who prior to taking office in June 2007 was chairman and CEO of Turner Corp., a multibillion-dollar global construction company. “We have to be actively recruiting foreign companies, foreign trade, and foreign investment.”
Mayor Leppert’s worldview underscores the global thinking taking place not just in Dallas but also throughout the entire North Texas area. Once labeled a one-industry region-think oil-the Dallas/Fort Worth Metroplex, as it’s called, is now a thriving, economically diversified part of the state that also happens to be among the most attractive places in the U.S. to start or expand a business. According to the Census Bureau, the Metroplex is one of the three fastest-growing metropolitan areas in the country. With a labor force of nearly three million people, it ranks third in the nation in annual employment growth. And the 12-county region, covering 9,000 square miles, is accessible to North America’s four major business cities; New York, Los Angeles, Toronto, and Mexico City.
Recognizing these strengths, 23 Fortune 500 companies have established headquarters in North Texas; not to name-drop, but the list includes Exxon Mobil, AMR (parent of American Airlines), Texas instruments, Kimberly-Clark, J.C. Penney, and Burlington Northern Santa Fe. In addition, during the past year, Fluor, Research In Motion (maker of the Blackberry), and Comerica Bank relocated their headquarters to North Texas, attracted by the region’s business-friendly stance and easy access to Dallas/Fort Worth International Airport.
There are other pluses, too. Companies located in the Dallas/Fort Worth area pay no corporate state income taxes and, according to the U.S. Commerce Department, Texas has one of the lowest state and local tax burdens in the country. And while areas in Florida, California, and the Northeast struggle with mounting home foreclosures. North Texas has dodged that particular bullet. “We didn’t see the big run-up in prices that many other parts of the country saw,” says Steve Golding, president of Jackson-Shaw, a real estate development company based In Dallas. “This area saw low single-digit increases. As a result we haven’t experienced that big drop in prices.”
In addition to retaining its strong position in oil and gas, North Texas has become a formidable presence in high tech, banking, air and rail transportation, health care, and retailing. The region is second only to Silicon Valley in terms of its technology-trained workforce, with 6,000 high-tech companies employing nearly 250,000 workers. Dallas/Fort Worth is also a major telecommunications hub, with the second-highest concentration of telecommunications manufacturing workers in the country. William Sproull, president and CEO of the Metroplex Technology Business Council (MTBC), the largest technology trade association n Texas, says he is always impressed by the strong image Texas projects in the U.S. and around the world. “It’s an area of the country that has always supported mavericks like Herb Kelleher [founder of Southwest Airlines] and Mark Cuban [owner of the NBA’s Dallas Mavericks], and businesspeople believe they can make money here.”
In early June, the MTBC hosted a program designed to seek out innovative technologies from a variety of individuals, universities, and small- and mediumsized businesses. Its partner in the event-which was called TechQuest-was chipmaker Texas Instruments. To help focus the submissions, Tl listed medical and health technology, energy management, and other such areas on the online application for the event. “We’re not looking to make these products,” says Mark Denissen, vice president of worldwide strategic marketing for Tl, “but rather to figure out if there is a potential business relationship between Tl and these smaller companies or individuals. We might fund the development of the technology, or even license it. The point is to foster innovative sourcing of new technologies right here in North Texas.” Fort Worth One of America’s fastest growing cities, Fort Worth is a thriving, dynamic community of 700,000-plus on the move. Still known as “Cowtown” -a reference to its colorful past as a major meatpacking hub on the Chisholm Trailtoday the city is a global business powerhouse that retains a small-town feel. It’s conveniently situated in the Central Time Zone at the crossroads of interstate highways and cross-country railways. Another plus is Fort Worth’s proximity to Dallas/Fort Worth International Airport and Alliance Airport, a first-of-its-kind, purely industrial aviation facility. This commercial infrastructure makes Fort Worth a major player on the international business stage.
Thanks to the diversity of the North Texas economy. Fort Worth continues to grow. The region boasts a highly skilled workforce, the ready availability of land and a supportive municipal government-just a few of the reasons that Fortune 500 companies and other large companies are moving to the city where the West begins.
While nonrenewable energy sources become scarcer globally, the region has found itself sitting atop the Barnett Shale, the largest natural gas field in Texas and one of the largest in the U.S. It’s an economic engine that is bringing new jobs to Fort Worth and bolstering the North Texas economy against uncertain times. And will for years to come.
Through its award-winning Sister Cities International program, Fort Worth has established strong international alliances with cities around the world and plans to expand to Canada as well as South and Central America. Fort Worth has also set its sights on China and will establish a sister city relationship there to strengthen ties and partner in its remarkable economic growth.
Despite its folksy charm, Fort Worth is a cosmopolitan city offering a quality of life second to none. Its cultural district boasts three world-class art museums-the Kimbell Museum, the Amon Carter Museum, and the Modern Art Museum. Other museums include the Fort Worth Museum of Science and History, undergoing a multimilliondollar renovation. Sundance Square, the city’s growing, exciting downtown, offers a wide array of restaurants, theaters, and nightspots plus the worldrenowned Bass Performance Hall. New buildings continue to rise as older ones undergo facelifts. Fort Worth’s renaissance is a result of the resurgence of commercial and retail development in the city’s core.
More than any other Texas city. Fort Worth has remained true to its Western heritage. A city with tomorrow in mind, Fort Worth honors its history and traditions while building for a bright, progressive future. Transportation Mecca Without question, the
Dallas/Fort Worth International Airport (DFW) is one of the biggest draws in North Texas. Spread over 18,000 acres, DFW handles 59 million passengers and nearly 700,000 flights a year, making it the third-busiest airport in the world. Despite its size-seven runways, five terminals, 1,900 daily flights, and the capacity to land four planes simultaneously-DFW is well-run, easy to navigate, and allows corporate executives to get in and out quickly.
“The growth of DFW and the growth of North Texas go hand in hand,” says Jeff Fegan, DFW’s CEO. When the airport was planned more than 3D years ago, the area between Dallas and Fort Worth was mostly prairie. Today the communities that ring DFW are thriving suburban enclaves with homes in every price range, and everyone from Starbucks to big-box retailers like Best Buy and Lowe’s are within a short drive.
While soaring energy costs are hurting many of the country’s airlines, DEW is well-positioned. A sizeable portion of its annual revenue-$640 million last year-comes from sources other than airlines, including concessions, parking, rents from commercial developments, and land leases. New royalties from natural gas drilling are being used to renovate DEW’s four domestic terminals and other key capital projects. DFW contributes some $16 billion to the local economy each year, making it the clear economic engine of North Texas.
The airport’s international terminal, completed in 2005, now draws about six million passengers a year, with a potential capacity of 14 million. Adding nonstop service to China would help get there. The mayors of Dallas and Fort Worth are pitching DFW as the ideal airport for Asian carriers, and American Airlines is expected to file for a China route in 2009. This year’s Open Skies agreement between the U.S. and the European Union has already paid dividends for DEW and the local economy, thanks to new service to London’s Heathrow on American and British Airways and daily nonstops to Amsterdam on KLM Royal Dutch Airlines.
Anyone who views railroads as a quaint throwback to a simpler time hasn’t been to Burlington Northern Santa Fe’s intermodal facility at Alliance Airport in Fort Worth. This sprawling 376-acre facility is a 24/7 hub of train and trucking activity designed to move freight from ports on the West Coast to locations throughout the U.S. More important, it positions the Metroplex as a key North American intermodal hub. “Rail is the most fuel-efficient way to move goods over ground,” says Steve Branscum, group vice president of consumer products at BNSE Railway, which is headquartered in Fort Worth. “And with the heavy traffic at West Coast ports due to an increase in Asian imports, it’s only going to make that scenario more common.”
To be sure, with 32,000 miles of track covering twothirds of the U.S., BNSF has felt the effects of the nation’s rising energy costs. Spending on fuel in just the first quarter of this year totaled nearly $1 billion, which is what the company spent during all of 2003. Still, even with higher fuel costs, the concern over ever-more-congested highways and greenhouse gas emissions from long-haul trucks lead transportation experts to say rail travel remains an attractive mode of transportation for companies that want to move their goods around the U.S. quickly and costeffectively.
At Alliance, a seemingly endless convoy of trucks drives into its intermodal facility each day, either to drop off or pick up the containers of freight that arrive on BNSF’s trains daily. With a completely automated system, says Joe Lumbert, hub manager at Alliance, truck drivers simply type in information about their vehicles and are then issued slips, detailing where they need to drop off their particular containers. On the other end of the facility are “strip tracks,” where the containers are parked. From there enormous cranes position themselves over the oneton containers and lift them onto or off the rail cars for delivery around the country. Alliance is BNSF’s fifth-largest intermodal facility in the U.S.; two larger ones are in Chicago and another two are in Los Angeles. In the area surrounding the complex, J.C. Penney, Coca-Cola, Hyundai, and other large companies have established huge warehouse and distribution centers, giving them easy access to rail transportation for their goods and contributing to the economic health of the region. “Alliance is our inland port,” says Fort Worth Mayor Mike Moncrief. “The growth in rail traffic there is a good indicator of growth in the whole region.”
Across the Metroplex, located 12 miles south of downtown Dallas, is the Dallas Logistics Hub. This 6,000-acre logistics park-being developed by The Allen Group, commercial development companysurrounds the Union Pacific intermodal facility that opened in October 2005. Dan McAuliffe, president of The Allen Group‘s Texas operations, says the logistics park will eventually contain 60 million square feet of retail, office, distribution, manufacturing, and warehouse space. Deep below 18 counties of North Texas lies the Barnett Shale formation, the largest natural gas field in the state and one of the biggest in the country. The field benefits North Texas in numerous ways and is responsible for pumping billions of dollars into not only the local economy but the entire state of Texas as well.
While the tight, black rock known as shale was formed from organic deposits over 300 million years ago, geoscientists didn’t figure out how to extract the natural gas inside the shale until the 1980s. Before then, drilling didn’t yield much gas. But over the years, with technological improvements in drilling techniques, Barnett Shale has proved to be one of the most prolific natural gas fields around.
One of the companies at the forefront of Barnett Shale drilling is Chesapeake Energy, the largest independent producer of natural gas in the U.S. Julie Wilson, vice president of corporate development for the company, says Chesapeake has been drilling in the Barnett Shale since 2004 and has pumped billions of dollars into local economies from its activities. Natural gas is clean, abundant, affordable, and American, and Chesapeake is providing a domestic energy source that can meet our nation’s energy needs.
A big beneficiary of that drilling is DFW International Airport, which receives annual payments for lease rights and royalties. Residents in Tarrant and Johnson counties are benefiting, too. According to Wilson, Chesapeake paid out $500 million in 2007 for lease rights to thousands of mineral owners whose property sits above the
natural gas field. Those mineral owners include schools, businesses, cities, and churches, and may be eligible for royalty payments ranging from $50 to thousands of dollars a month, depending on the amount of land they own. Advances in drilling, Wilson is quick to point out, mean that Chesapeake is able to establish drill sites in urban areas, and can drill several horizontal wells from one padsite, thereby reducing its environmental footprint.
Devon Energy is another big driller and the largest natural gas producer at Barnett Shale. John Richels, president of the company, says Devon has drilled more than 1,300 wells since 2002 and now accounts for nearly half of the field’s overall daily production. “Barnett Shale is such an important resource to this area,” he says. “It’s generating billions of dollars for local economies and is responsible for thousands of new jobs.”
While the direct payments to the region are staggering, the indirect benefits are substantial as well. A March 2008 report on the economic impact of Barnett Shale shows that activity from drilling added an additional $8.2 billion to the North Texas economy in 2007 and created 83,823 new jobs. Of course, growth of this nature creates stresses. “Barnett Shale is benefiting everyone by creating new jobs and new businesses,” says Fort Worth Mayor Mike Moncreif, “but the challenge is keeping up with that growth.” Building new roads and schools to accommodate the increases in the workforce connected to Barnett Shale means that some new roads don’t even have street signs yet, says the Mayor. “We welcome the growth, but we want it to be responsible growth,” he cautions.
To ensure that it happens. Fort Worth has developed strict municipal ordinances. These laws determine where and when drilling can be done and detail what local communities can expect from companies like Chesapeake and its competitors. For instance, says Mayor Moncrief, instead of making just lease and royalty payments to a community for the right to drill in its backyard. Fort Worth and surrounding areas are encouraging, and in some instances requiring, beautification efforts by these companies. “We are pushing the energy companies to give back to the community, which may include adding something like a new walking trail in an area where they are drilling,” he says. “The companies understand they are more apt to be welcomed back if they’re helping to keep up the neighborhoods where they’re drilling. We like to call this doing business the Fort Worth way.”
Fortifying the robust economic health of North Texas is a rich and varied quality of life. The area offers affordable home prices, a solid public school system, and cultural and sporting events to satisfy every taste. Dan Petty, president and CEO of the North Texas Commission (NTC), a nonprofit dedicated to promoting the economic health of North Texas, points to a new opera house and performing arts center in downtown Dallas, and to Bass Hall and the Texas Motor Speedway in Fort Worth, as some of the more notable cultural and recreational hotspots in the region.
The Metroplex also boasts nearly 30 colleges and universities, including Southern Methodist University, University of Dallas, Texas Christian University, Texas Wesleyan University, and the University of Texas system, which is active in making grants for high-tech development.
The Dallas Cowboys, who play football in Texas Stadium in nearby Irving, lead the roster of big-time sports names. Professional hockey, basketball, and baseball teams also do their thing in North Texas. And much to the delight of government and business officials, the region recently won out over scores of other U.S. cities to host the 2011 Super Bowl. A new stadium in Arlington is being constructed-complete with a retractable roof-for the big day. Based on recent Super Bowls in other cities, says the NTC’s Petty, the event and the days leading up to it are expected to bring $500 million of spending into the region.
As with any region experiencing rapid growth, North Texas faces its own set of challenges. Estimates show the area’s population mushrooming from six million to nine million over the next 20 years. Such growth puts a strain not only on the area’s infrastructure but on its natural resources as well. Dallas Mayor Leppert says he’s proud that earlier this year the Environmental Protection Agency listed his city as the nation’s top municipal purchaser of renewable energy. The city, he says, is getting 40% of its 2008 energy needs from renewable resources, primarily wind power.
Mayor Moncrief of Fort Worth points out that with such rapid population growth, the region can’t build roads fast enough. He is working with other government officials and business leaders to establish a light-rail system-similar to the one now used in Dallas-to help ease the transportation squeeze. “There will be some kind of light-rail service in Fort Worth sooner rather than later,” he vows.
Putting it all together, North Texas stands out as a vibrant, diversified region of the country with a cando attitude and a larger-than-life vision that seems to be an ingrained part of the state’s DNA. “We don’t do anything small here,” says a lifetime resident of North Texas. “If it’s worth doing, we do it big-and we do it well.”
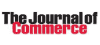
Target reconsiders supply-chain strategy
July 14, 2008
Target reconsiders supply-chain strategy
By Peter TirschwellAs many of the nation’s largest retailers, including Wal-Mart, have embraced inland ports accessed via rail as a core component of their supply-chain strategy, the nation’s No. 2 container importer. Target Stores, has gone its own way. It has held firmly to a strategy of routing most of its imported merchandise through a handful of import distribution centers located on the East and West coasts, and relaying goods by truck or rail to the regional DCs that feed its 1,600 retail locations.
This has made Target’s supply chain responsive to the whims of customer demand because it allows the company to take control of goods immediately upon disembarkation from the ship and opportunistically divert them to areas of robust demand. But at a time of skyrocketing fuel costs, Target is realizing that flexibility has its price.
Jim Theusch, Target’s senior corporate real estate manager, appeared to confirm that a change in thinking is under way at the company, which ranked No. 2 in the JoC Top 100 Importer listing for 2007, with 435,000 TEUs brought into the United States. “We will need to look at inland port locations at some point in time,” he said in a speech at the recent JoC Real Estate Logistics Forum in Chicago.
The sharp rise in fuel prices over the past year, last week’s 6 percent drop notwithstanding, has sent logistics managers across the country back to their spreadsheets to recalculate the impact and develop alternatives. If there was a day when rent at DCs or inventory carrying cost was the driver of strategy, that day has come and gone. Now it’s about minimizing exposure to high fuel costs. More often than not, that means keeping goods moving on the cheapest form of transportation for as long as possible, whether that means using all-water services versus West Coast transload, or West Coast rail to an inland port.
“The key issue is, how far can we get into the interior and not change a mode, and if we have to change a mode, we want it to be from water to rail. That is now becoming much more important,” said Curtis Spencer, president of Houston-based IMS Worldwide.
This emphasis plays into the hands of railroads and developers of logistics parks built around inland railheads. A tightly integrated system in which containers arrive intact via rail and then are drayed only a short distance to an inland import DC, is finding a lot of interest as importers hone in on the fuel cost impact of every leg of the supply chain, said Richard Allen, CEO of the Allen Group.
Spencer said Theusch’s statement was an “acknowledgement of the value of the inland port concept taking the container on the cheapest transportation mode closest to the population centers.”
But others caution not to take the impact of fuel prices out of proportion. Changes are coming, but they are most likely to be on the import end of the supply chain. Importers may open East Coast import DCs, route more goods via rail and or make greater use of third-party DC operators that allow them to implement a shift in strategy faster than if they had to build and manage a facility on their own.
But immovable realities remain no matter how high oil prices climb. Customers, for the most part, live where they live, which is why retail locations have been built up in specific places to serve them. Whether the goods move via all-water Panama Canal or intermodal rail, basically the same retail network must be served by whatever supply-chain approach is adapted. 1 don’t know if anyone is suggesting that the basic model in which one regional DC serves 50 to 80 stores is poised for a
major overhaul.
“For larger retailers that have multiple DCs around the country or globally, fuel is a concern, but they are not going to make wholesale changes to their supply chain as a result of the increase in fuel. We haven’t had discussions with our customers that would suggest that,” said Anthony Chiarello, senior vice president of AMB Property Corp. “Where they may have an opportunity might be to move from a single import DC in Southern California to two to three DCs. We’re seeing that fuel in those instances is becoming a more significant metric when they are making those decisions.” So the point, for the moment, is to watch the import end of the supply chain. That is where changes will likely be seen first.
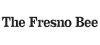
Warehouses at home in Tulare Co.
June 13, 2008
Warehouses at home in Tulare Co.
By Bob Rodriguez
Tulare County is fast becoming the latest central San Joaquin Valley community to attract large-scale distribution warehouses to the region. Paul Saldaña, president and chief executive officer of the Tulare County Economic Development Corp., said companies are drawn to the area by its affordability, central location and cooperation of city officials.
Saldaña said the EDC is working with eight companies that have expressed interest in locating to Tulare County.
“We are getting more attention, and we expect that to continue,” Saldaña said.
Officials with real estate firm Grubb & Ellis/Pearson Commercial said there are several companies looking for 1 million-plus square feet in Tulare County.
“This is a great area because of its location,” said Lou Ginise, a senior vice president with Grubb & Ellis/Pearson Commercial’s industrial division. “People want to avoid the congestion of the Inland Empire and Northern California. And when land prices go up elsewhere, that also gives us an advantage.”
Tulare County already is home to several large-scale industrial parks with the capability of expanding to meet the massive square footage needs of distribution centers.
And more space could be on the way. Tulare city officials have identified a 272-acre site south of Mefford Field airport for industrial and manufacturing use.
“We are very happy with our agricultural base, but we also recognize that we are on the main line of Union Pacific and on 99 and that is ideal for manufacturers and distribution centers,” said Bob Nance, Tulare’s redevelopment director.
The most recent distribution center to locate to Tulare County is the International Paper Co.
The company recently moved to a new 252,040-square-foot center in the MidState 99 industrial park at Goshen Avenue and Plaza Drive in Visalia.
A Fortune 100 company, International Paper is a global supplier of uncoated paper and packaging materials.
Built by the Allen Group, MidState 99 also built two industrial buildings near International Paper that total 280,000 square feet and are available for lease. The MidState 99 industrial park has 11 buildings with more than 3 million square feet of space. The tenants include, VF Corp., JoAnn Stores, Coast Distribution Systems, Workflow One, Worms Way, Bound Tree Medical and DATS Trucking.
Also building on a large scale is the Fresno-based Diversified Development Group. Last year, the company built a 500,000-square-foot distribution center for Spectrum Brands in its Plaza Drive Industrial Park in Visalia. From Visalia, the company ships batteries, personal-care products and home and garden items to seven western states.
Developers say that businesses can reach more than 65 million consumers within a two-day truck run from Visalia.
And as the price of fuel continues to rise, transportation costs are becoming a bigger factor in choosing a new location.
“These days, deals are done on a transportation-related basis,” said Jon Cross, marketing director for the Allen Group.